CPM Precision setzt bei der additiven Fertigung die Pulverbettfusion ein. Bei diesem Verfahren wird aus dem Ausgangspulver Schicht für Schicht ein Bauteil mittels Lasertechnologie aufgeschmolzen.
Durch das Auftragen von hauchdünnen Schichten aus Titanpulver auf eine Grundplatte wird das Bauteil nach und nach aufgebaut.
Diese äußerst präzise, innovative Methode ist für Prototypen und die Serienherstellung gleichermaßen geeignet.
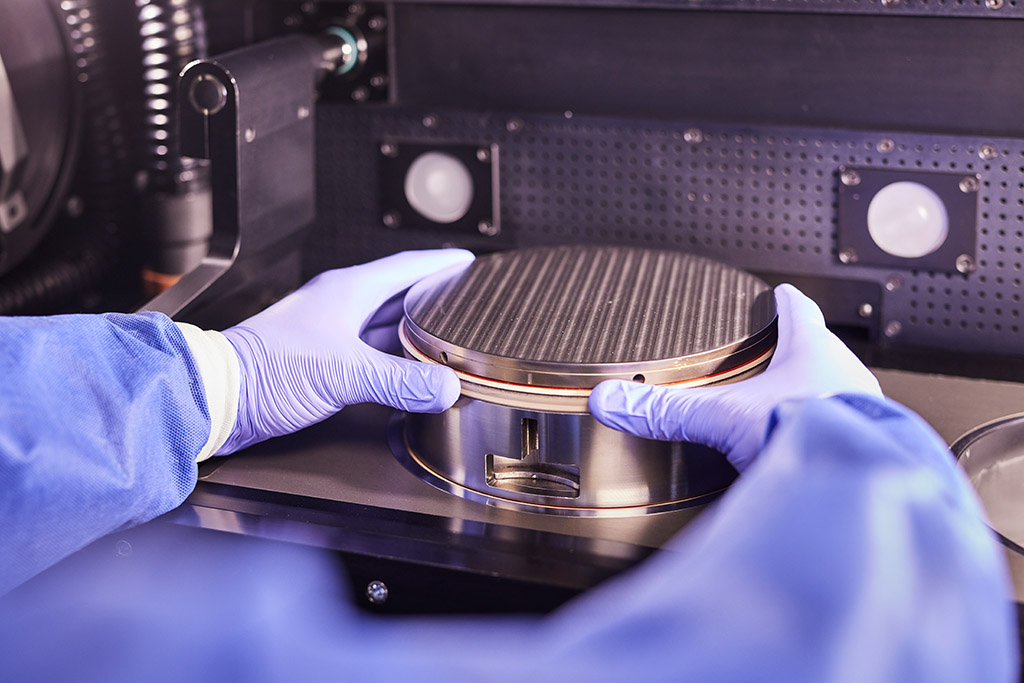
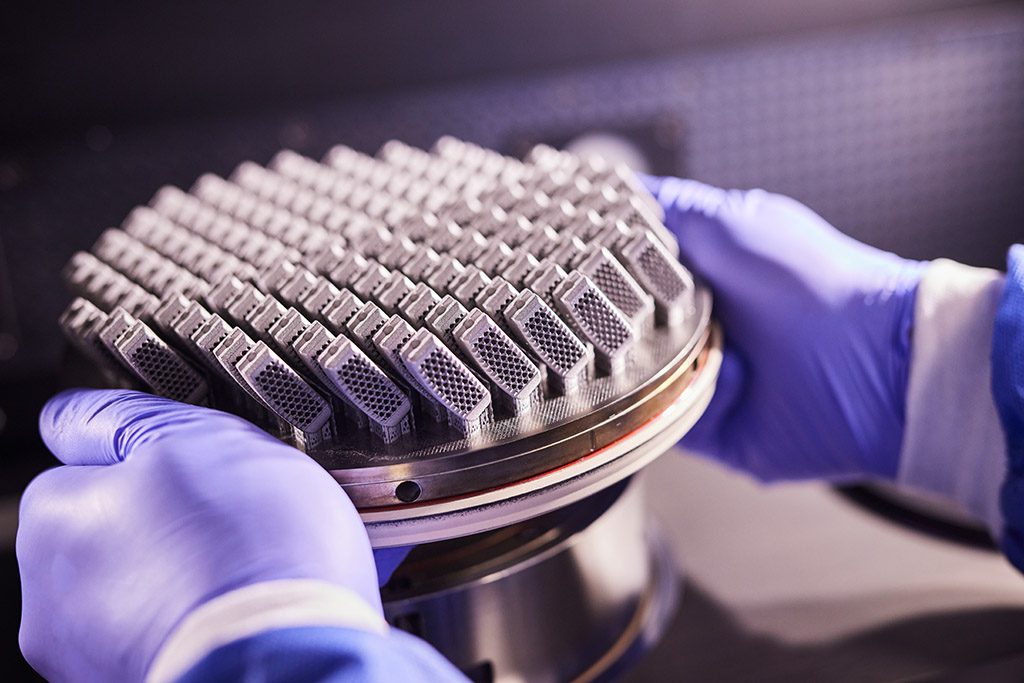
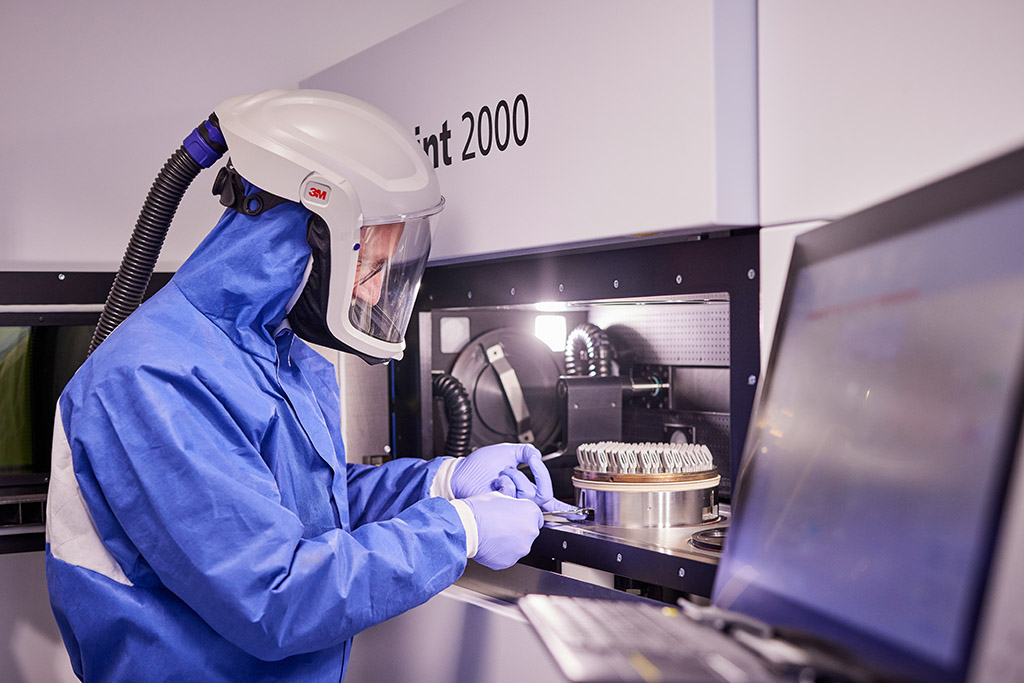
Im Entwicklungsprozess entwerfen wir mittels einer geeigneten CAD-Software eine Bauteilekonstruktionsvorlage. Im nächsten Schritt erstellt der 3-D-Drucker schichtweise das geplante Bauteil. Selbst auf Sonderfälle sind wir eingestellt: Neben Neuentwicklungen können die CPM Precision-Experten ein bereits bestehendes Bauteil als Vorlage verwenden. Beim sogenannten Reverse Engineering importieren wir den Entwurf in eine Slicer-Software; diese erstellt die nötigen Anweisungen für die Fertigungsmaschine.
Der gängige Begriff für die additive Fertigung ist der 3-D-Druck – doch in der Präzisionssprache ist es das PBF/LBM-Verfahren. Dieses innovative Produktionsverfahren eröffnet unserer Industrie völlig neue Möglichkeiten. Bereits seit 2015 setzen wir auf diese Zukunftstechnologie; zahlreiche erfolgreiche Projekte bestätigen mit qualitativ hochwertigsten Ergebnissen diese Ausrichtung.
- Es können vollständige Baugruppen komplett gefertigt werden, die Montage entfällt.
- Die Anzahl an Einzelteilen pro Baugruppe wird reduziert – und damit auch die Nachbearbeitungs- und Montagezeit.
- Viele Medizintechnik-Konstruktionen profitieren von der Geometriefreiheit, beispielsweise bei porösen Wirbelsäulencages, die dank makrostrukturierter Oberflächen eine bessere Knochenanlagerung erreichen.
- Topologieoptimierte Geometrien werden mit dem 3-D-Drucker 1:1 gefertigt. Dabei lässt sich die Bauteilsteifigkeit (z.B. von Implantaten) als Parameter einstellen.
- Neue Ideen oder Veränderungen lassen sich ohne großen Rüstaufwand an der Maschine erstellen, wodurch schnelle Prototypenschleifen möglich sind.
- Die Methode ist kostengünstig, gerade dann, wenn komplexe Strukturen angefertigt werden sollen.
Gewicht
Materialverbrauch
Montageaufwand
Bauteilzusammenführung/
-reduktion
Kosten
Funktionsumfang
Sie wünschen große Bauteile oder hohe Stückzahlen? Können wir. Der Kern unseres innovativen Technologieparks zur formlosen Fertigung ist unser leistungsstarker Drucker mit Faserlasern. Damit setzen wir zylindrische Projekte mit einem Durchmesser von bis zu 200 mm und einer Höhe von ebenfalls 200 mm um. Das bedeutet: Auch große Bauteile sind realisierbar. Je nach Bauteilgröße lassen sich so hohe Projekt-Stückzahlen realisieren.
Die Multilaser arbeiten gleichzeitig – ein weiteres Plus für eine wirtschaftliche Fertigung und eine deutliche Zeitersparnis. Der Laserdrucker trägt in der CPM Precision-Produktion Schichten auf, die lediglich 20 μm dick sind. Diese sehr feinen Schichten bieten einen besonders hohen Detailgrad, beispielsweise bei der Oberflächenbeschaffenheit. Die anschließende Wärmebehandlung übernimmt ein Kammerofen unter Schutzgasatmosphäre. Die Pulvervorbereitung sowie das gesamte Pulver-Handling erfolgt unter Schutzgas.
Falls eine Weiterbearbeitung erforderlich wird, setzen wir auch hier auf maschinelle Lösungen mit neuesten Maschinengenerationen wie beispielsweise auf CNC-Kurzdreh-, CNC-Langdreh- und CNC-Fräsmaschinen.
Sie sehen: Es gibt viele Möglichkeiten – wir zeigen diese gerne in einem Gesprächstermin auf. Hier geht’s zur Beratung.
Mit unserem Qualitätsanspruch setzen wir auch in der additiven Fertigung Maßstäbe. Gerne erläutern wir unsere Qualitätskriterien an konkreten Beispielen:
Das gesamte Pulverhandling findet zu 100% unter Ausschluss von Umgebungssauerstoff statt. Intelligente Monitor- und Softwarelösungen überwachen den gesamten Bauvorgang minutiös. Nach jeder einzelnen Schicht, welche die Multilaser auftragen, erfolgt die Prozesskontrolle. Bei diesem validierten Prozess nutzen wir das Powder Bed Monitoring und weitere Methoden. Sensoren erfassen alle relevanten Daten. Deren Auswertung ermöglicht es uns, frühzeitig mögliche Fehler zu erkennen und schnell zu reagieren. So haben wir die gesamte Produktion stets im Blick und erfüllen unsere hohen Standards in Bezug auf Sicherheit, Effizienz und Qualität.
Die additive Fertigung ist eines der modernsten Verfahren in der fertigenden Industrie. Bauteile lassen sich mit dieser Technologie schnell, günstig und flexibel produzieren und werden dabei ebenfalls höchsten Materialanforderungen gerecht.
Profitieren Sie von unserer umfassenden Erfahrung und entdecken Sie die Vorteile des additiven Fertigungsverfahrens. Nehmen Sie Kontakt mit uns auf. Wir beraten Sie gerne.
Was ist die additive Fertigung?
Additive Fertigung bzw. additive manufacturing, kurz AM genannt, ist der Oberbegriff für Fertigungsverfahren, die Werkstücke Schicht für Schicht aufbauen, anstatt wie bei anderen Verfahren von einem Materialblock mittels Zerspanung abzutragen und so das Bauteil herauszuarbeiten. Verwendet wird das Verfahren in nahezu allen Industriebranchen, die Metall-, Keramik- und Kunststoffbauteile herstellen. Gerade für die komplexen Anforderungen der Medizintechnik ist das Fertigungsverfahren besonders gut geeignet und bietet zahlreiche Vorteile.
Additive Fertigung vs. konventionelle Fertigung – welche Methode ist besser?
Dank unseres modernen Maschinenparks bieten wir sowohl die spanende als auch die additive Fertigung an. Somit sind wir methodisch breit aufgestellt und auf komplexe Produktionen vorbereitet. Jedes Verfahren bringt Vorteile mit sich. So kann die additive Fertigung Material, Zeit und Energie einsparen und einen großen Funktionsumfang abdecken. Die spanende Fertigung wiederum punktet nach wie vor mit höchster Genauigkeit und flexiblen Anwendungsmöglichkeiten. Unsere hochqualifizierten Fachkräfte mit langjähriger Expertise in beiden Fertigungsbereichen helfen Ihnen gerne bei der individuellen Auswahl. Auch eine Kombination beider Verfahren ist möglich.
Welche additiven Verfahren verwendet CPM Precision?
Unter dem Oberbegriff additiver Fertigungsverfahren werden mehrere, ähnliche Produktionsweisen zusammengefasst. Die Unterscheidung erfolgt nach methodischen Details in der Herstellung
- Pulverbettverfahren, etwa das Laserschmelzen oder auch PBF/LBM: Ein pulverförmiger Werkstoff wird per Laser schichtweise und selektiv aufgeschmolzen.
- Flüssigmaterialverfahren, z.B. Stereolithografie: Hier härtet der Laser Harz, gemischt mit dem gewünschten Werkstoff, aus.
- Freiraumverfahren, zum Beispiel das Schmelzschichtungsverfahren Fused Deposition Modeling (FDM): Ein Drucker mit beheizbarer Düse bewegt sich frei im Raum (daher die namensgebende Bezeichnung) und lagert feinste Stränge des Werkstoffes ab, die anschließend aushärten.
Wir nutzen zur Herstellung hochwertiger Medizintechnikprodukte das Laserschmelzen, auch unter dem Kürzel PBF-LB/M bekannt. Dieses Verfahren ist ideal, um Bauteile zu produzieren, die spezifische Oberflächenbedingungen erfüllen müssen und gleichzeitig eine hohe dynamische und thermische Belastbarkeit gewährleisten. PBF-LB/M ermöglicht es, komplexe Geometrien mit dünnwandigen Flächen durch das Direktverschmelzen des Ausgangsmaterials zu erzeugen.
Welche Materialien verwendet CPM Precision in der additiven Fertigung?
Unsere Medizinprodukte aus der additiven Fertigung werden ausschließlich aus Titan hergestellt. Das garantiert höchste Reinheit. Wir verwenden Titan Grade 4 und 23. Letzterer entspricht Grade 5, ist aber speziell für höhere Anforderungen, wie sie in der Medizintechnik auftreten, geeignet. So überzeugt die Legierung mit ihrer guten Biokompatibilität und bringt ausgezeichnete Eigenschaften mit. Verglichen mit Titan Grade 5, besitzt Grade 23 eine besonders hohe Reinheit. Die interstitiellen Elemente sind reduziert – das verbessert sowohl die Bruchzähigkeit als auch die Duktilität des Materials. Zudem hat die Legierung ein geringes Eigengewicht. Sie ist damit optimal geeignet für chirurgische Implantate oder kieferorthopädische Geräte.
Übrigens: Die Qualifizierung unserer Druckparameter für Titan Grade 4 ist nicht selbstverständlich und in der Branche keineswegs üblich! In Zusammenarbeit mit unserem Maschinenhersteller Trumpf haben wir als Erstanwender die Laserparameter für Reintitan Grade 4 qualifiziert und somit unser Fertigungs-Know-how auf höchstem Niveau erweitert.